A high efficiency air filtration system removes contaminants that interfere with processes. Air intake filtration helps eliminate particulate that can clog essential process equipment and foul product.
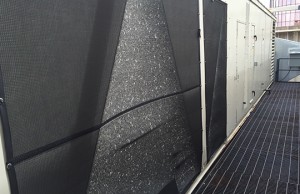
Filters such as this one provide an efficient and cost-effective solution for air intake filtration. It can be used outdoors, year-round and can be easily mounted on existing equipment by in-house maintenance staff.
Manufacturers engaged in process cooling or other applications where temperature control is critical may experience elevated energy costs on a regular basis. Also, the potential for dust and other environmental particulates clogging the cooling system or hindering robotic assembly can result in high maintenance costs, reduced productivity and excessive downtime.
The best solution, of course, is to prevent the systems from shutting down in the first place. In this article, learn how high efficiency air filtration equipment can be an effective solution to many of these challenges.
Environmental Contaminants
Keeping cooling systems clean can be difficult. Because many of the systems depend on air drawn from outside of a facility, environmental contaminants will likely be present — and can easily become problematic.
While air intake nuisances vary by season and climate, contaminants are universally frustrating. Insects, cottonwood, leaves, crop-harvest debris and pollen are only a few examples of what manufacturers must contend with. In time, these particles can build up and settle within the cooling system, adversely affecting cooling performance while diminishing the longevity of sub-components like heat exchangers and coils.
Some businesses choose to rely on chemical treatment programs to prevent these problems. While this option certainly can help reduce the presence and impact of particulates in a cooling system, keeping high volumes of foreign matter at bay while remaining compliant with chemical treatment regulations can be difficult. Another option to consider is air-intake filters that prevent contaminants from ever entering the system.
Air Intake Filtration
Regardless of the technology used to process air being pulled inside a system or facility, air intake filters can effectively prevent contaminants from compromising a cooling system. Typically, air intake filters are installed on existing equipment, where fresh air enters into the system. They filter debris before it can become a problem to fins, coils or high efficiency interior filter banks. Air intake filters can be installed on cooling towers, air-cooled chillers, condenser units and most other fresh air intake openings.
Benefits associated with air intake filters include:
- Minimizing debris entering the system.
- Protecting fill material and cooling water.
- Extending the life of internal filters.
- Eliminating downtime caused by clogged systems.
- Increasing efficiency of cooling systems.
- Reducing energy costs by keeping system running efficiently.
- Preventing sludge buildup in water basins.
- Reducing the need for coil cleaning solvents.
Much like indoor air filtration systems, air intake filters can be customized for a facility’s specific equipment needs. Air inlet or outlet challenges can require pipe or electrical cutouts, special shapes and frame, media or mounting options. From small condenser and chiller coils to large cooling towers and intake openings, air intake filtration systems can protect valuable equipment from airborne debris. Experienced filter specialists can help determine what will work best for specific application challenges.
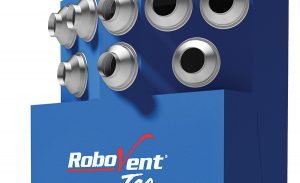
When installing these filters, be mindful that process cooling cycles include continuous water trickling down within cooling towers and are susceptible to ice formations in the winter months.
Filtration Can Help Improve Indoor Air Quality
When discussing process cooling applications, indoor air quality is not often a primary consideration. However, nearly every industrial process has challenges that need to be met in order to keep products, equipment and staff safe.
For example, pharmaceutical manufacturing is under enormous regulatory pressure and held to the highest standards of purity and accuracy. Excess dust is unacceptable, so the management of airborne dust in the pharmaceutical manufacturing process is a necessity. Dust capture while manufacturing silica chips is essential as well. The tiniest foreign particles can render silica chips unusable. Therefore, capturing those dusts during the manufacturing process it critical.
Much like pharmaceutical manufacturing, the food processing industry is held to high standards for the health and safety of not only employees but also the public who will be consuming those products. Dust, mist, smoke and fumes in the manufacturing process must be contained in order to keep products pure in a temperature-controlled environment.
Robotic operations are becoming increasingly popular in manufacturing. Applications like robotic welding can create vast amounts of fumes and particulates that need to be removed through advance robotic weld-fume extractions. While robotic assembly systems typically do not generate harmful particulates, the systems can be negatively impacted by dusts present in a facility. Dust makes the equipment less efficient, less precise and can cause unexpected downtime for maintenance issues.
Chemicals, rubber and injection moldings are all temperature-sensitive applications and are susceptible to the complications that come with poor indoor air quality.
For some types of manufacturing, simply blowing contaminated air to the outside and pulling outdoor air inside may be adequate. But, when processes require strict indoor temperature control and the minimization of outdoor contaminants, exhaust and makeup air systems may have disadvantages, including:
- Increased environmental contaminants pulled into a facility.
- Additional stress on process cooling and comfort heating and cooling equipment.
- Inconsistent temperatures expediting corrosion on equipment.
- Higher energy costs.
- Environmental compliance issues.
- Decreased comfort for personnel.
A high efficiency air filtration system keeps heated or cooled air in the facility while removing contaminants that are harmful to people or interfere with processes. In these temperature-controlled situations, air filtration systems could be the better option.
Source Capture vs. Ambient Air Filtration Systems
Source capture systems capture harmful dusts and fumes at the point of creation. This keeps dust from permeating throughout a facility and wreaking havoc on air quality and equipment. Ambient air filtration systems are intended to clean and circulate the air throughout an entire facility.
High volume operations that produce a lot of dust or fumes are best served with a source capture solution. Welding, grinding and blasting are such examples. Failing to utilize source capture systems in these processes would be very dangerous for employees, equipment and products in a manufacturing facility.
Facilities with operations spread across a wide area, especially when the air contains lower volumes of contaminants may be better served with an ambient air filtration system. These systems ensure that contaminants do not linger and threaten workers. Applications that deal with fewer toxic substances are good candidates for ambient capture as well.
Utilizing high efficiency air filtration systems rather than traditional push-pull ventilation systems makes it easier to maintain consistent indoor temperatures, which in turn reduces stress on process cooling equipment.
Cleaner air helps equipment maintain its integrity and keeps the overall system performing as intended. While these systems work together to optimize equipment and personnel performance, the results can include decreased downtime, increased uptime and healthier environments (both physically and financially).
Because all manufacturing environments have their own products, processes, contaminants and challenges, it is a good idea to work with an experienced air quality engineer to find the best solutions for each individual facility.
This blog was contributed by Eugene Beck, Rensa Filtration, as published in Processing Cooling Magazine July 1, 2019